When it comes to efficient dust and fume collection, Electrostatic Precipitators (ESPs) have long been a go-to solution across a wide range of industries. However, choosing between a Dry ESP and a Wet ESP isn’t as straightforward as it may seem.
Each system has its strengths, limitations, and industry-specific applications. So, how do you decide which type is right for your plant?
In this guide, we’ll compare Dry and Wet ESPs across critical factors like performance, application suitability, operating environment, maintenance needs, and cost-effectiveness, helping you make an informed decision for your emission control strategy.
Электростатикалық тұндырғыш (ESP) дегеніміз не?
An Electrostatic Precipitator is an advanced filtration device that removes fine particles, such as dust, smoke, and mist, from a flowing gas using the force of an induced electrostatic charge.
Both Dry ESPs and Wet ESPs work on this principle, but their construction, method of particle collection, and use cases differ significantly.
What is a Dry Electrostatic Precipitator?
A Dry ESP removes solid particulate matter from flue gas using ionization. The charged particles are attracted to oppositely charged collection electrodes and then removed via mechanical rapping (vibration) that causes the dust to fall into a hopper.
Key Characteristics:
Used for solid particles like fly ash, cement dust, and coal dust
Particles are removed dry, without water or scrubbing
Typically installed downstream of boilers, kilns, or incinerators
Requires rapping mechanisms to dislodge collected dust
What is a Wet Electrostatic Precipitator?
A Wet ESP functions similarly to a dry ESP but is used for wet, sticky, or soluble particles. Instead of rapping, particles are flushed from the collection plates using water, making it ideal for capturing fine mists, aerosols, and fumes that would otherwise escape a dry collection system.
Key Characteristics:
Ideal for submicron particles, mist, metal fumes, acid droplets, and sticky dust
Uses water sprays to wash particles off electrodes
Common in industries with high-moisture or corrosive gases
Eliminates dust re-entrainment due to wet collection
Біздің шешімдер ауқымын ашыңыз:
Side-by-Side Comparison: Dry vs. Wet ESP
Criteria | Dry ESP | Wet ESP |
---|---|---|
Particle Type | Dry, solid particulates | Wet, sticky, corrosive, or submicron particulates |
Cleaning Method | Mechanical rapping | Continuous water flushing |
Collection Efficiency | High for coarse dust (PM10) | Superior for ultrafine particles (PM2.5 and below) |
Техникалық қызмет көрсету | Requires rapping system upkeep | Needs water management & corrosion control |
Жұмыс шарттары | Dry gas flows, moderate temperatures | Moist or saturated gas streams, low temperature |
Installation Areas | Boilers, cement kilns, incinerators | Chemical plants, smelters, FGD scrubbers |
Capital Cost | Жалпы төмен | Higher initial cost due to corrosion-resistant design |
Ongoing Costs | Lower (no water usage) | Higher (due to water and corrosion management) |
Which Industries Prefer Dry ESPs?
Dry ESPs are the preferred solution in industries where emissions are primarily dry dust particles. These include:
Cement Manufacturing – for kiln and clinker cooler dedusting
Coal-Fired Power Plants – for fly ash removal
Pulp & Paper Industry – for boiler flue gas filtration
Steel & Metal Processing – for furnace exhaust
Waste Incineration – for high-temperature particulate control
Their low operational costs and reliable performance in dry environments make them a go-to solution for particulate removal in bulk material industries.
Where Do Wet ESPs Excel?
Wet ESPs are ideal for situations where emissions include acidic gases, sticky compounds, or ultrafine mist and fumes that traditional dry systems struggle to capture.
Industries where Wet ESPs are commonly used:
Non-Ferrous Metal Production – zinc, copper, aluminum smelting
Chemical and Petrochemical Plants – for removal of oil mists and acid droplets
Glass Manufacturing – for lead and cadmium mist control
Food Processing – where steam and organic aerosols are emitted
Flue Gas Desulphurization (FGD) Systems – for polishing stages
Their ability to handle wet and submicron pollutants while ensuring zero re-entrainment makes them invaluable in these sectors.
Электростатикалық сүзгілер
Key Decision Factors: Which One is Right for You?
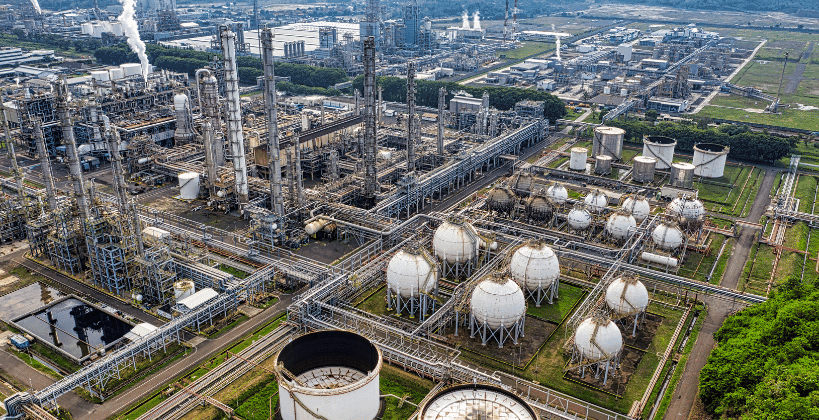
Choosing between Dry and Wet ESP depends on several plant-specific factors:
1. Nature of Emissions
The composition and physical state of your emissions are the most fundamental considerations.
- Dry ESPs are best suited for applications that produce dry, free-flowing particulate matter, such as fly ash, cement dust, or metallurgical fumes. These particles are typically coarse and can be easily dislodged using mechanical rappers.
- Wet ESPs are the ideal choice when dealing with fine, sticky, oily, or wet particulates, such as acid mists, metallic aerosols, or condensable organics. These are typically found in exhaust streams from chemical plants, smelters, and wet scrubber outlets. The use of water to wash down the collection surfaces makes Wet ESPs more effective in handling these challenging emissions.
2. Gas Stream Characteristics
The temperature, moisture content, and chemical composition of your process gas have a direct impact on the performance and durability of an ESP system.
- Dry ESPs perform optimally in high-temperature, low-moisture gas environments, such as those generated in cement kilns, coal-fired boilers, and incinerators. These systems are designed to withstand heat and maintain performance without corrosion.
- Wet ESPs are built for saturated, low-temperature, and corrosive gas flows, where water vapor or chemical compounds might condense and cause issues in dry systems. These systems are constructed with corrosion-resistant materials like stainless steel or high-grade alloys to prevent deterioration.
3. Desired Efficiency Level
Different industries have different compliance benchmarks, especially with the growing focus on ultra-low emissions.
- Dry ESPs are highly efficient in collecting larger particles (e.g., PM10), often achieving up to 99% removal efficiency for coarse dust.
- Wet ESPs, on the other hand, are unmatched in removing ultrafine particulates (PM2.5 and below), aerosols, and condensable fumes. They can achieve ultra-low emission levels, making them the technology of choice where stringent environmental norms are enforced.
4. Maintenance Considerations
Each ESP type comes with unique maintenance needs, which should align with your plant’s manpower, infrastructure, and downtime tolerance.
- Dry ESPs require regular maintenance of rappers, electrodes, and hoppers, and occasional cleaning to ensure uninterrupted dust removal. They are mechanically intensive but well-understood by most plant operators.
- Wet ESPs need continuous water circulation, spray nozzles, and drainage systems to flush out particles. Proper water chemistry management is essential to prevent scaling or biological fouling. Corrosion monitoring is also critical, especially with aggressive gas compositions.
5. Budget Constraints
Cost is always a factor, but it must be weighed against the long-term performance, environmental benefits, and operational savings.
- Dry ESPs typically involve lower capital investment and simpler operating costs, particularly in applications with dry and predictable particulate matter.
- Wet ESPs generally require higher upfront investment due to corrosion-resistant materials, water circulation systems, and added complexity. However, in environments where dry collection is inefficient or leads to higher maintenance, Wet ESPs offer better reliability and lower emissions-related risk.
Intensiv Filter Himenviro: Your ESP Solution Partner
Whether your plant needs a robust Dry ESP for dust-heavy processes or a precision Wet ESP for mist and fume control, Intensiv Filter Himenviro provides tailor-made systems to meet your environmental and operational goals.
Why Choose Us?
Decades of ESP design and engineering expertise
- Proven installations across cement, power, chemical, and metal industries
- High-efficiency, CPCB/NGT-compliant solutions
- Global delivery and lifecycle support
- Retrofitting and upgradation services are available for existing plants
Our ESP solutions are engineered to deliver not just compliance, but reliability, durability, and peace of mind.
Need Help Choosing the Right ESP?
Every plant is different. Emissions, process conditions, and environmental goals vary. That’s why we don’t believe in one-size-fits-all solutions.
Let our experts help you determine the right technology for your plant, backed by engineering insights, emissions audits, and real-world performance data.