Smarter Filtration. Better Operations. Lower Costs.
Filter bags are the unsung heroes of dust collection systems. Whether in cement, metal processing, chemicals, pharmaceuticals, or power plants, filter bags serve as the frontline defense against particulate emissions. But when these bags fail prematurely, the consequences are far-reaching—unexpected shutdowns, rising maintenance costs, production losses, and even compliance risks.
The good news? With the right approach, you can significantly extend filter bag life while reducing operating costs. This isn’t just about maintenance—it’s about operational intelligence.
The True Cost of Filter Bag Failure
Filter bags wear out due to multiple operational stressors. Abrasive dust particles grind down fabric surfaces. Chemical fumes degrade fibers. Excessive temperatures melt or harden media. Even something as basic as incorrect cleaning pulse settings can shorten bag life dramatically.
Each of these problems, if left unchecked, leads to a chain reaction: reduced filtration efficiency, higher emissions, increased pressure drop, and more frequent replacements. These costs add up quickly.
Understanding the causes of failure is the first step toward building a more resilient filtration system.
طیف وسیعی از راه حل های ما را کشف کنید:
1. Selecting the Right Filter Media
The foundation of filter bag longevity lies in choosing the right filter media. Industrial processes vary widely in temperature, chemical exposure, and particulate characteristics. A one-size-fits-all approach doesn’t work.
For instance, standard polyester bags are suitable for dry, low-temperature dust environments but will degrade quickly in high-heat or corrosive gas streams. In such cases, aramid (نومکس), PPS (Ryton), or PTFE-laminated fiberglass bags offer better thermal and chemical resistance.
Choosing a media that matches your application ensures the bags can withstand the environment without compromising filtration performance.
2. Optimizing the Pulse-Jet Cleaning System
Your filter bags are only as effective as the cleaning system that keeps them operating. Pulse-jet cleaning removes accumulated dust cake using compressed air bursts—but it must be done correctly.
If the system pulses too frequently, the fabric suffers unnecessary wear. If it pulses too little, dust buildup causes airflow restriction and increased differential pressure. Striking the right balance, often through differential pressure-based cleaning control, helps preserve the structural integrity of the bags.
It’s also crucial to maintain proper nozzle alignment and air pressure calibration. Misdirected pulses or inconsistent flow can damage bags or reduce cleaning efficiency.
3. Managing Dust Loading and Distribution
Uneven or excessive dust loading can overwhelm certain sections of your baghouse, leading to localized wear and shortened bag life. High-velocity dust streams can also erode bag surfaces on impact.
Introducing inlet baffles or deflection plates helps slow down and evenly distribute incoming dust, minimizing abrasive damage. Duct design and air velocity must be optimized to prevent turbulence and dead zones where dust might accumulate.
These adjustments may seem minor, but they have a major effect on how evenly bags wear over time.
4. Controlling Moisture and Temperature
Moisture is one of the most common enemies of baghouse performance. When process gas temperatures fall below the dew point—particularly in the presence of acid gases—condensation occurs. This leads to blinding (clogging) of filter media and corrosion of supporting components.
Maintaining process gas temperatures above the acid dew point is essential. This can be achieved through insulation, pre-heating systems, or by improving combustion controls. For high-humidity or chemically aggressive environments, filter bags with PTFE membranes or other moisture-resistant coatings offer greater protection.
Proper temperature and moisture control not only extends bag life but also enhances overall collection efficiency.
5. Practicing Predictive Maintenance and Inspection
Routine inspections and predictive maintenance programs can help detect issues early—before they result in major failure. This includes checking for bag tears, seam ruptures, excessive dust cake buildup, or physical damage from broken cages or misaligned venturis.
Monitoring differential pressure is a critical performance indicator. A gradual rise in pressure suggests dust accumulation or blinding, while sudden drops may indicate a leak or rupture.
Instead of waiting for failures to happen, develop a preventive maintenance schedule that includes planned shutdown inspections, bag rotation strategies, and cage replacement when necessary.
6. Ensuring Proper Installation and Handling
Even the highest-quality filter bag can fail if installed incorrectly. Bags must be mounted with the correct tension—not too loose, which causes abrasion, and not too tight, which stresses seams.
Proper gasket sealing is vital to prevent air leakage and dust bypass. Matching the bag with an appropriate, undamaged cage prevents premature damage due to contact or vibration.
Training your maintenance team or engaging professional service providers for installation can eliminate many of the most common causes of early failure.
7. Leveraging Smart Filtration Monitoring
Today’s filtration systems benefit immensely from digital intelligence. Sensors, PLCs, and cloud-based monitoring tools can provide real-time insights into airflow, differential pressure, cleaning frequency, and even early leak detection.
Such systems not only improve bag life but also help optimize energy consumption by avoiding unnecessary pulsing. In many plants, the implementation of smart monitoring has led to a measurable reduction in compressed air use, energy savings, and fewer unplanned maintenance events.
Real-World Impact: Better Bag Life, Lower Operating Costs
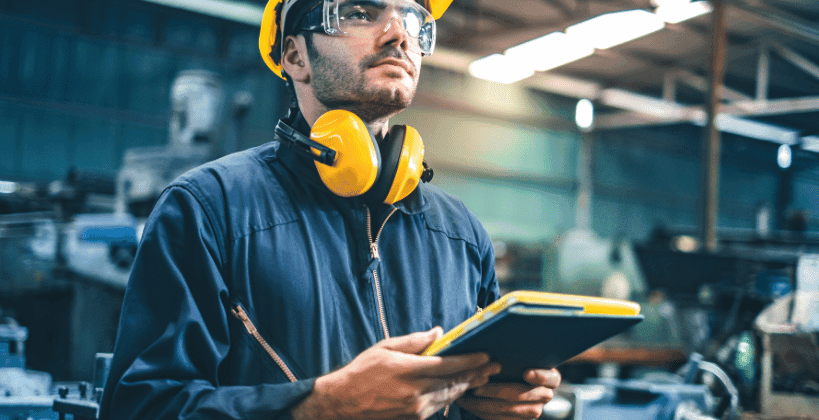
When all of these strategies come together, the result is transformational. Plants that adopt proactive maintenance and proper system design often report:
Up to 40% longer filter bag life
20–30% savings in compressed air used for cleaning
Fewer emergency shutdowns due to bag failures
Enhanced regulatory compliance with consistent PM levels
Improved total cost of ownership for baghouse systems
For industries operating under tight margins and strict environmental norms, this is not just an operational win—it’s a strategic advantage.
اکنون با ما در ارتباط باشید
Intensiv Filter Himenviro: Your Partner in Long-Lasting Filtration
At Intensiv Filter Himenviro, we specialize in designing and servicing high-performance baghouse systems tailored to your plant’s specific requirements. With decades of expertise and a global footprint, we help industries reduce emissions, improve filter longevity, and lower lifecycle costs.
From choosing the right filter media to optimizing your cleaning system, our team ensures every aspect of your filtration solution is built for endurance and efficiency.
Final Thought
The longevity of your filter bags is not just a maintenance concern—it’s a reflection of your plant’s overall operational health. By understanding the science behind filtration and applying practical, data-backed solutions, you can turn your baghouse from a cost center into a performance asset.
Want to assess your current filter bag performance or plan an upgrade?
Contact Intensiv Filter Himenviro today for expert consultation and filtration audits designed to extend your bag life and boost your bottom line.