Filtros regenerables
Los sistemas de separación son básicamente separadores de gravedad, separadores centrífugos, separadores húmedos, separadores eléctricos y separadores de filtración entre los que puede elegir. Los separadores de filtración se dividen en filtros de almacenamiento y filtros regenerables, siendo estos últimos los que desempeñan un papel dominante en la categoría de separadores de filtración debido a sus ventajas. El amplio léxico intensivo de filtros para la eliminación de polvo proporciona información detallada sobre los filtros regenerables.
Características del Filtro Regenerativo
Los llamados filtros regenerables se utilizan para separar partículas sólidas de los gases cuando se deben limpiar altas concentraciones de aire de escape cargado de polvo (hasta 200 g/m³). El efecto de limpieza se basa en la llamada filtración de superficie. Las partículas se separan principalmente en la superficie del medio filtrante en la capa de partículas (torta de polvo) que se forma. Después de alcanzar una caída de presión especificada o en intervalos fijos, los medios filtrantes se limpian para que el proceso de filtración pueda repetirse periódicamente. El polvo separado puede recuperarse.
Los diseños de filtros regenerables difieren en la disposición geométrica del medio filtrante, el flujo de gas y el tipo de limpieza.
Otra subdivisión de los separadores filtrantes se basa en el tipo y el embalaje del material filtrante. En cuanto al tipo de medio filtrante, se hace una distinción entre filtros de bolsa, filtros de bolsa, filtros de cartucho, filtros de láminas y filtros de casete.
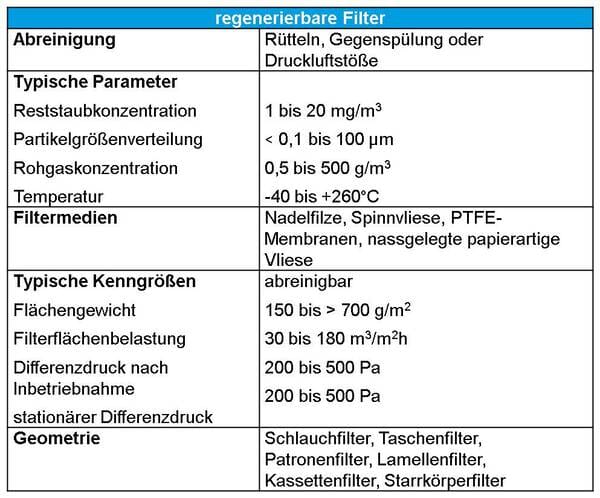
Geometría de filtros de mangas, filtros de mangas, filtros de cartucho, filtros de láminas y filtros de casete
- En los filtros de bolsa, el elemento filtrante suele ser una bolsa cilíndrica. Las mangueras filtrantes se fabrican en diferentes diámetros y longitudes. Los filtros de bolsa se utilizan para filtrar el aire de escape a temperaturas bajas y medias de hasta aprox. 250 °C; el tejido de la bolsa retiene el polvo que fluye a través de ellas. Las mangueras filtrantes se limpian periódicamente, generalmente mediante pulsos de aire comprimido. El efecto de limpieza del pulso de aire comprimido se intensifica adicionalmente mediante el inflado repentino de la manguera filtrante. Por lo tanto, los filtros de bolsa son especialmente adecuados para polvo pegajoso o muy adhesivo.
- Los filtros de bolsa se utilizan para eliminar el polvo de pequeñas cantidades de gas. El medio filtrante se extiende sobre un marco plano en forma de placa, abierto por un lado para la salida del gas limpio. El flujo se realiza de fuera a dentro. Las bolsas de filtro se limpian periódicamente, generalmente mediante pulsos de aire comprimido. El efecto de limpieza del pulso de aire comprimido se intensifica adicionalmente por el inflado repentino de la bolsa de filtro. Este efecto es solo mínimamente menor con el filtro de bolsa que con el filtro de bolsa. Por lo tanto, los filtros de bolsa también son especialmente adecuados para polvo pegajoso o muy adhesivo.
- Los filtros de cartucho son una alternativa cada vez más popular a los filtros de bolsa. El medio filtrante se pliega en forma de estrella y se coloca sobre una cesta de soporte cilíndrica. El flujo se produce desde el exterior hacia el interior y la limpieza se realiza mediante un golpe de presión o un lavado a baja presión. Los filtros de cartucho solo se utilizan para polvo que sea fácil de limpiar, de lo contrario, los pliegues se obstruirían con polvo.
- Los filtros de láminas son una alternativa a los filtros de mangas. Se colocan dos medios filtrantes plegados uno sobre otro y se pegan o se sueldan entre sí en sus puntos de contacto. El flujo se realiza desde el exterior hacia el interior y la limpieza se realiza mediante un golpe de presión o un lavado a baja presión. Los filtros de láminas se utilizan únicamente para polvo que sea fácil de limpiar, de lo contrario, los pliegues se obstruirían con polvo.
- En los filtros de casete (filtros HEPA), el gas cargado de polvo entra normalmente en la cámara de gas bruto de la carcasa del filtro por la parte inferior, donde se produce la separación previa, y fluye primero a través de la primera etapa de filtrado. El polvo fino que se arrastra se separa en el exterior de los pliegues del casete de filtrado. El casete de filtrado se limpia neumáticamente. Un tubo de boquillas se mueve lentamente de un lado a otro a lo largo y ancho del casete de filtrado. El aire comprimido sopla el cartucho de filtrado hacia abajo y libera los elementos filtrantes del polvo. El gas limpio de la primera etapa de filtrado puede fluir opcionalmente a través de una segunda etapa de filtrado sin limpiar (filtro de seguridad, filtro policial).
¿Cómo funcionan los separadores filtrantes?
El gas cargado de partículas fluye generalmente desde el exterior a través de los elementos filtrantes: el filtrado se deposita en el exterior del medio filtrante a través de la corriente de aire. Se forma una capa de polvo, la denominada torta de filtración. El medio filtrante debe limpiarse periódicamente.
Para la limpieza, la torta de polvo se desprende de nuevo mediante impulsos cortos de aire comprimido o movimientos mecánicos de agitación, mediante un contralavado con aire o impulsos cortos de aire comprimido.
La capa de polvo cae, por ejemplo, en un embudo colector que se vacía periódicamente (por ejemplo, a través de una válvula giratoria).
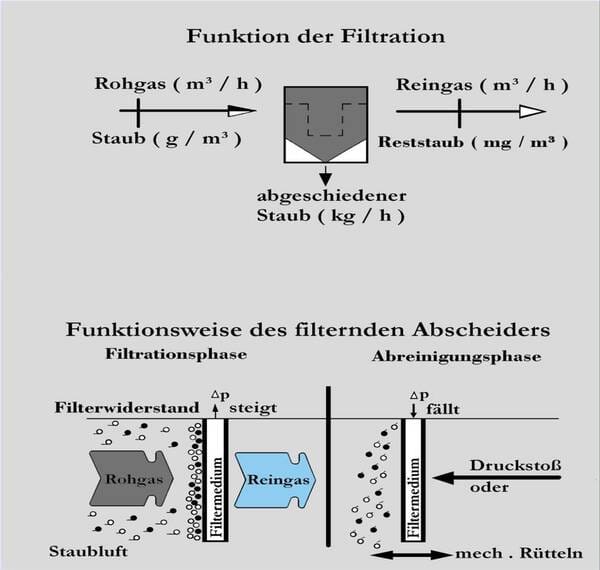
Separadores filtrantes de rendimiento operativo
El comportamiento operativo depende de un gran número de factores influyentes: estructura del sistema de filtrado, tipo y diseño del medio filtrante, modo de funcionamiento del sistema, propiedades de las partículas y propiedades del gas portador.
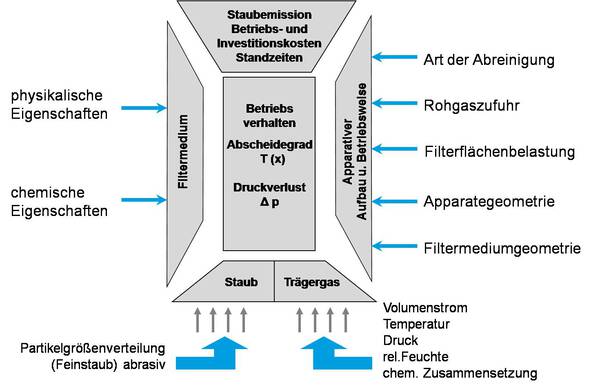
Mecanismos de limpieza Separador de polvo
Durante la separación mecánica de partículas de polvo y gas en el elemento filtrante, la capa de polvo que se acumula en la superficie del elemento filtrante crea una presión diferencial (resistencia del filtro). Para evitar superar una determinada presión diferencial (normalmente < 1.500 Pa), los elementos filtrantes deben limpiarse periódicamente.
Además de la forma y la disposición del medio filtrante, el tipo de limpieza es la característica central del diseño de un filtro. El movimiento mecánico del medio filtrante, la inversión del flujo de gas, la transferencia de momento a la torta de filtración y las combinaciones de estos mecanismos se consideran mecanismos de limpieza.
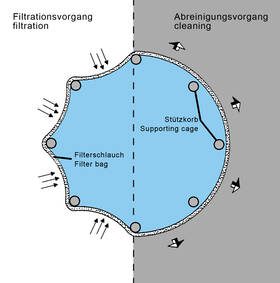
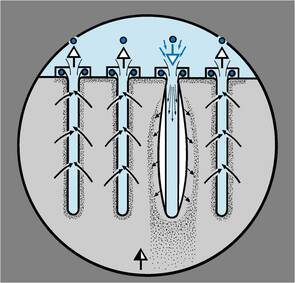
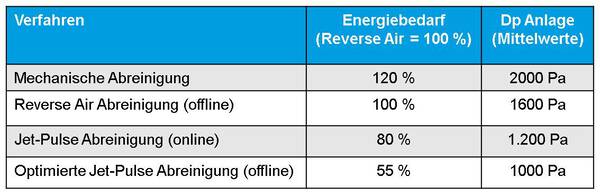
Filtro regenerativo con limpieza mecánica
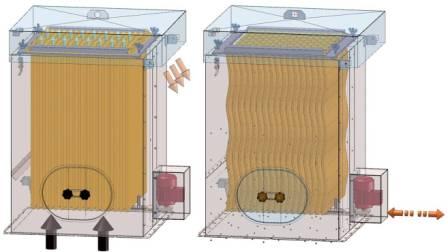
Los medios filtrantes se someten a un gran esfuerzo mecánico durante la limpieza mediante agitación. Dado que los filtros vibratorios solo pueden funcionar de forma discontinua y, por lo tanto, no están diseñados para un uso continuo, los medios filtrantes pueden tener una vida útil de hasta 5 años, y en raras ocasiones incluso hasta 7, según el modo de funcionamiento.
Filtro regenerativo con limpieza por retrolavado
La limpieza por contracorriente se utiliza para medios filtrantes mecánicamente sensibles (p. ej., casetes de filtro) que se dañarían al agitarlos o limpiarlos con chorro de aire. La limpieza se lleva a cabo mediante una inversión de flujo parcialmente dirigida, en la que el medio filtrante se va soplando gradualmente desde el lado del gas limpio, la masa de polvo se desprende y se transporta hacia abajo. En este caso, la limpieza también se puede realizar solo fuera de línea.
El sistema de filtrado suele estar diseñado en varias cámaras y se limpia cámara por cámara (limpieza fuera de línea). Debido a su bajo estrés mecánico, los medios filtrantes pueden tener una vida útil de varios años.
La forma más utilizada y moderna de limpieza de los separadores de filtración es el método de chorro de aire comprimido (limpieza por pulsos de chorro). Este tipo de limpieza se ha convertido en la norma. En los sistemas Jet-Pulse, la limpieza se lleva a cabo mediante un chorro intenso de aire comprimido que invierte repentinamente la dirección del flujo, provocando que los elementos filtrantes se hinchen brevemente y que la torta de filtración se desprenda mediante transmisión de impulsos.
Durante la fase de filtración, el material filtrante (p. ej., mangueras o bolsas) se hace pasar desde el exterior hacia el interior; un bastidor de soporte proporciona al elemento la estabilidad necesaria. En función de la cantidad de polvo, la limpieza se realiza mediante golpes de presión cada 1 a 10 minutos; normalmente se regula midiendo la presión diferencial del filtro.
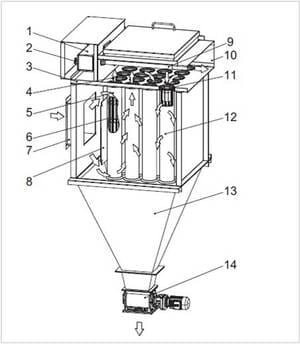
- Tanque de aire comprimido
- Válvula de diafragma
- Piso intermedio para alojar el medio filtrante
- Cámara de gas limpia
- Manguera filtrante
- Cesta de apoyo
- Entrada de gas crudo
- Placa deflectora para distribución del flujo de gas
- Boquilla de palo
- Salida de gas limpio
- Boquilla de entrada
- Manguera de filtro durante la limpieza
- Sala de recolección de polvo
- Descarga de polvo
Diseño estructural de separadores filtrantes
Los separadores de filtración constan básicamente de:
- Cabezal de filtro con dispositivo de regeneración (hoy en día, normalmente limpieza con aire comprimido)
- Piso intermedio para alojar los elementos filtrantes
- Elementos filtrantes
- Alojamiento
- sala de recolección de polvo
- Descarga de polvo en diferentes versiones
- Componentes adicionales, p. ej. control de limpieza, órganos de descarga, etc.
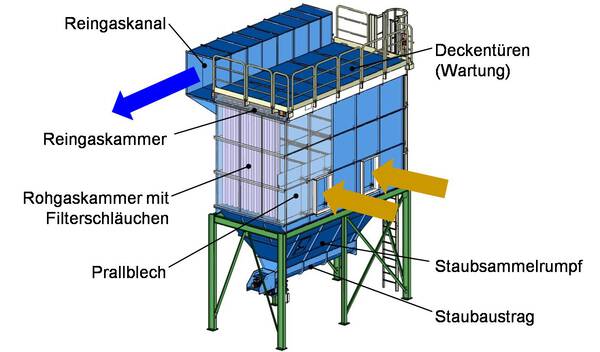
Parámetros de diseño típicos para filtros con limpieza mecánica, limpieza por contralavado y limpieza por pulsos de chorro
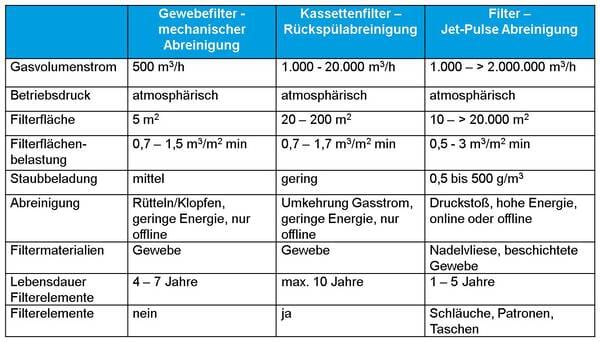